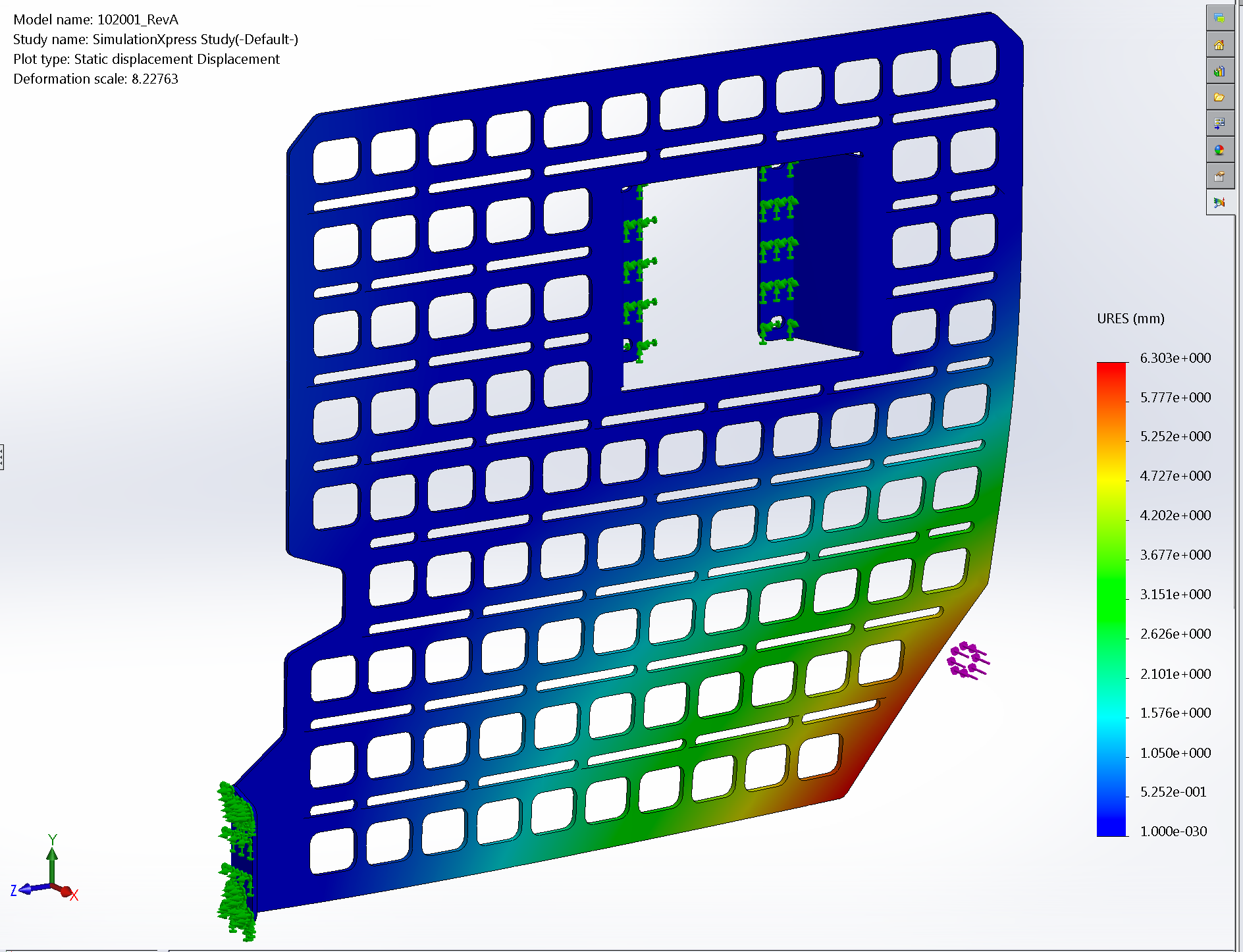
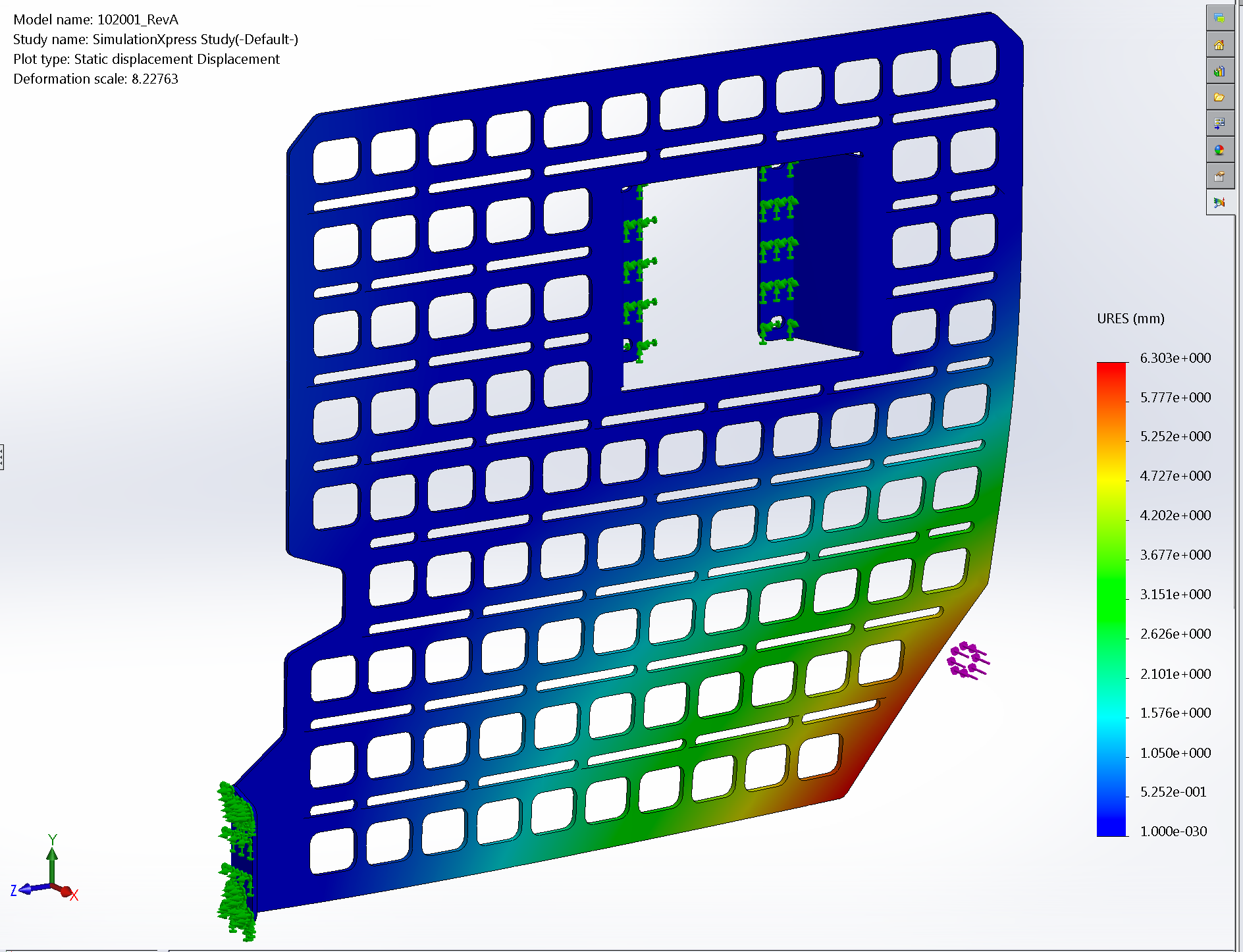
The bed of a pickup truck has historically been a featureless storage space with only a few tie down points for whatever you’re hauling and that’s it. In 2015, Ford introduced the Boxlink system in their F-150, Raptor and SuperDuty lineup, which offers mounting cleats for accessories and such, but most of those accessories are single purpose (pictured below). The bedsides of the truck bed still offer little to know way of storing tools, gear and other equipment in an organized fashion and without occupying valuable ‘floor space’ in the bed.
This dilemma is what lead to the development of the Bedside Rack System for the 2015 and newer Ford F-150 and Raptor. I was on my way to pick up a pallet of freshly zinc-plated steel brackets for our Rear Seat Release product line and when I got to their shipping dock, I realized that I still had a small Rubbermaid tub of tie downs, 5gal gas can and garden shovel sliding around from some yard work the previous weekend. Not only was this unsafe, but it also prevented us from easily loading the pallet into the truck. I needed to awkwardly stack the gas can and shovel on top of the pallet after loading and carry to tub inside the cab back to our shop.
That’s no big deal, but what could I have done to save time and frustration? That’s when the idea for our Bedside Rack System was born. We got to work 3D scanning the inner bed of the truck and designed prototypes for basic function testing. During that time, we worked with Ford to receive that actual 3D CAD data for each truck we were intending to design for, to ensure easy installation and a perfect fit every time. The 2015, 2016, 2017 and 2018 F-150 beds all feature four Boxlink mounting points along with four independent tie-down points. Provided our engineering is spot on to allow great fitment, these should offer a good deal of strength.
With a general design, we set out to prototype the system. Our initial prototypes were CNC plasma cut and hand formed. They fit and functioned well enough to test durability and general function. We loaded them up with Quick Fist clamps and various shovels, jacks, fuel cans and so on. They took whatever we threw at them.
Because we know some users will carry heavier jacks, like the Pro Eagle Jack or air compressor setups, like the ARB compressor setup in their Ford truck, we tested heavier loads both with 45lb plates and using computer simulation. The computer simulation demonstrated that while there we had plenty of safety factor and little risk of failure we did see deformation of the portion of the panel that’s relatively unsupported. The addition of a rubber bumper to brace the cantilevered portion of the panel against the bedside worked perfectly to prevent this deformation and reduce strain.
With this, we moved into production with confidence!
(Click here to read part 2 of 3 – The Manufacturing Process)
Introducing: Quick Fist Clamps - You asked!
Don't know what to buy an F-150/Raptor Owner for Christmas? - 2017 Holiday Gift Guide